Remote Service and Monitoring for Large Machine Fleets
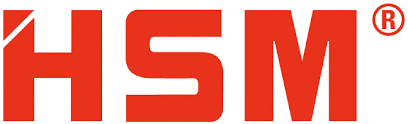
CASE STUDY
Remote service and monitoring for large machine fleets
Meeting the challenge to remotely manage a geographically dispersed and complex range of baling presses, from large fully automatic systems to small presses, each with distinct technological requirements.
OVERVIEW
The rapidly growing fleet of different HSM machines across multiple customer sites was a challenge for cost effective and efficient operations and maintenance. As part of their commitment to customer service, HSM aimed to streamline remote servicing capabilities and enable efficient data monitoring for both large and small presses. This was vital for supporting operational efficiency, preventing unplanned downtimes, and aligning with emerging customer demands for digitized billing processes, none of which could be delivered with existing technology.
DEVELOPING THE M2M SOLUTION
Collaborating with service and product management, HSM’s automation department sought a universal M2M platform. They required a solution to provide remote service functions, comprehensive remote capabilities, secure networking, data visualization, and integration with existing tools. They chose Ardexa’s platform due to its versatile capabilities and robust security.
ABOUT HSM
Hermann Schwelling Maschinenbau (HSM) is a pioneering company in environmental and office technology, specializing in baling presses for compaction of recyclable materials. With a rich history dating back to the introduction of their first baler in 1972, HSM has evolved into a global leader, offering a diverse range of equipment with cutting-edge technology.
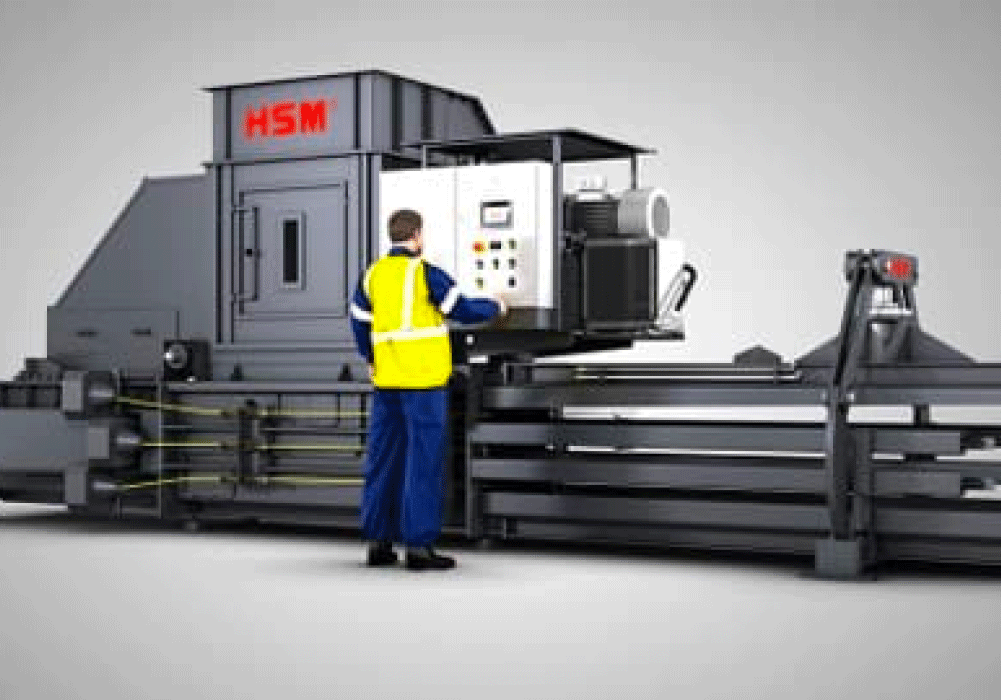
To meet HSM needs, a Proof of Concept (PoC) was crafted. Ardexa deployed its application to facilitate remote access, ensuring both security and functionality. For communication with Siemens S7 PLCs, a plug-in was configured, serving as a bridge between the presses and the cloud platform. Implementing the solution for both large and small presses was a critical milestone, especially considering the vast data generated by continuous operation.
ENHANCED AND PROACTIVE SERVICE
Following successful pilot testing, the Ardexa M2M solution was integrated as a standard feature in all new machines.
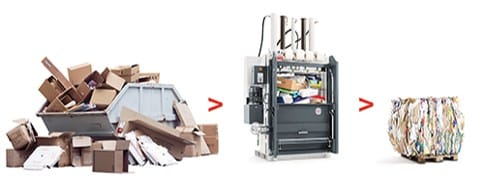
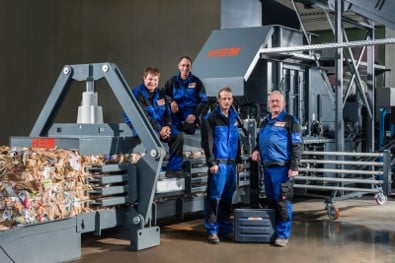
Customers gained access to customizable dashboards for their presses, managed by HSM’s power users. HSM’s service department could now monitor and manage all presses from a single interface.
The fine-tuned access system allowed selective remote actions, while recording and analyzing data became more efficient. Software updates and fault management could be remotely executed. Furthermore, the data collected laid the foundation for proactive service measures, anticipating and addressing issues before they impacted operations.
-
UNIFIED CENTRAL CONTROL
-
FLEXIBLE USER MANAGEMENT
-
SECURE REMOTE MAINTENANCE
-
ANALYSIS AND REPORTING TOOLS
-
INTERFACE TO 3RD PARTY TOOLS
-
ADVANCE CYBERSECURITY SUITE
-
REAL-TIME DATA CAPTURE
-
CUSTOMISABLE ALERTS
-
COST EFFECTIVE IoT GATEWAYS
-
COMPATIBILITY TO EXISTING SYSTEMS
DRIVING EFFICIENCY AND FUTURE GROWTH
HSM’s collaboration with Ardexa resulted in a transformative solution that streamlined remote servicing, empowered data-driven decision-making, and positioned the company as a digital pioneer in the industry. By offering comprehensive remote service capabilities and harnessing data insights, HSM enhanced operational efficiency, minimized downtime, and set the stage for future digital service innovations.
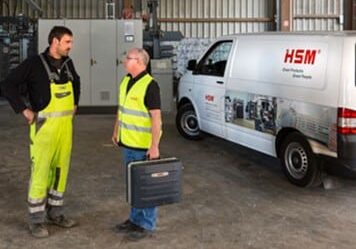