SCADA vs. Digital Control Platforms: Why Renewable Energy Needs a New Approach
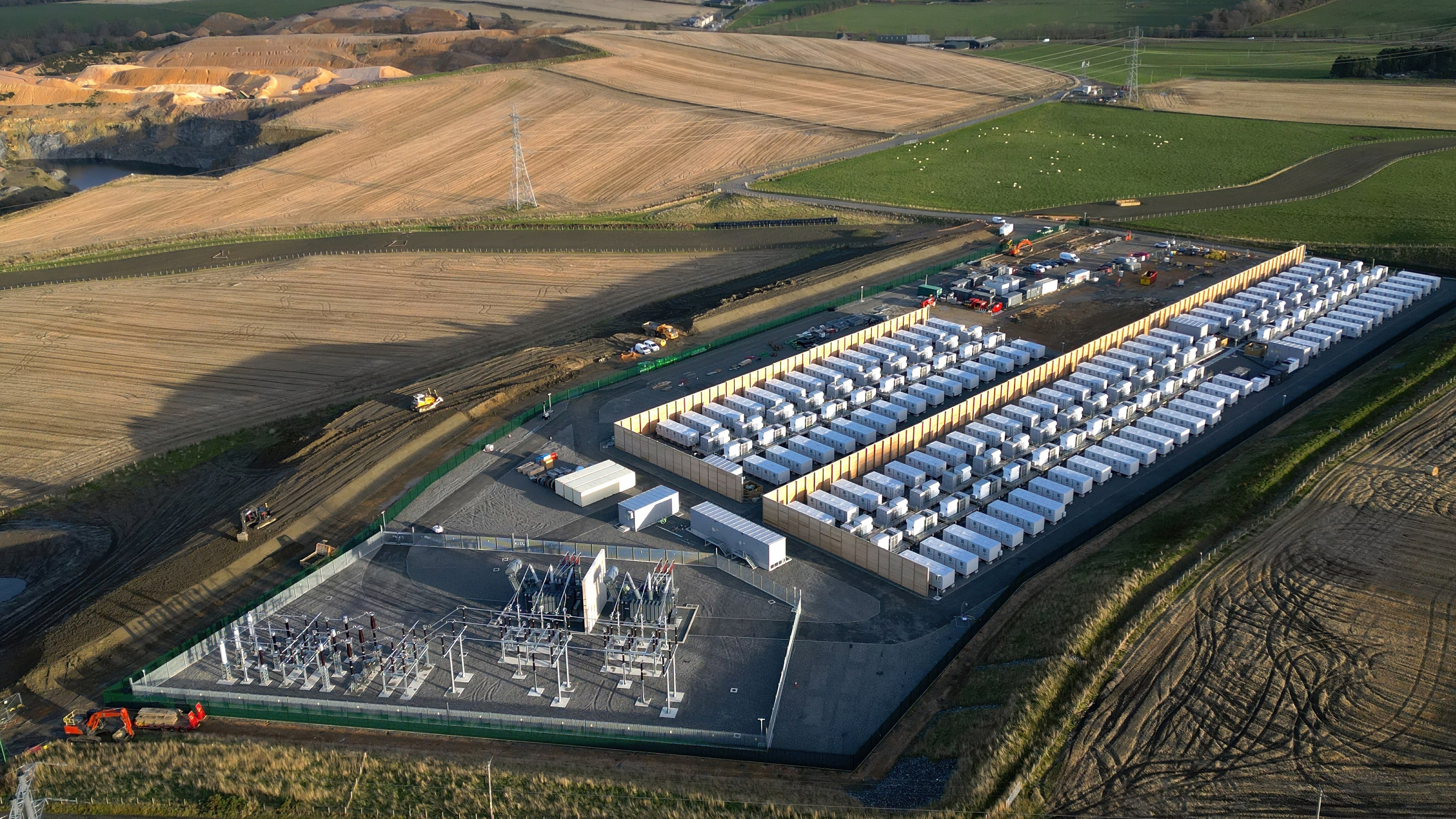
PART 1
SCADA vs. Digital Control Platforms: Why Renewable Energy Needs a New Approach
The renewable energy industry has a problem: it’s trying to operate 21st-century distributed energy infrastructure using control systems designed for 20th-century manufacturing plants. Traditional SCADA systems, born on factory floors with physical security perimeters and round-the-clock technical staff, are fundamentally mismatched to renewable energy’s operational reality—hundreds of unmanned sites scattered across vast territories, operating under strict cybersecurity mandates, with razor-thin margins demanding operational efficiency.
This mismatch isn’t just inconvenient—it’s becoming a competitive liability. As regulatory requirements tighten, cyber threats multiply, and operational complexity increases, the limitations of legacy SCADA systems are forcing renewable operators into expensive workarounds, vendor dependencies, and operational constraints that undermine long-term competitiveness.
The emergence of Digital Control Platforms represents more than just technological evolution—it’s SCADA reinvented for the modern era. Born from the Industrial Internet of Things movement and cloud-native architecture principles, DCPs fundamentally rethink how distributed energy assets should be monitored and controlled, addressing the specific operational challenges that traditional SCADA systems were never designed to handle.
The Manufacturing Floor Legacy: Where SCADA Began
To understand why traditional SCADA systems struggle in renewable energy applications, it’s essential to recognise their origins and the operational assumptions built into their DNA.
SCADA systems were designed for manufacturing plants with robust physical security perimeters, controlled access, and skilled technicians available 24/7/365. Even large manufacturers typically operate a handful to a couple dozen major facilities, making custom programming and site-specific configurations economically viable.
These systems were developed when air-gapped networks provided sufficient protection, and cybersecurity was primarily a physical access control problem. Built for on-premise deployment using proprietary hardware ecosystems, they assume dedicated hardware, on-site maintenance, and limited need for remote integration.
Traditional SCADA systems require significant on-site configuration and specialised expertise for setup, modification, and maintenance. SCADA vendors built closed ecosystems using vendor-specific controllers, interfaces, and programming tools, creating customer dependencies that were manageable in manufacturing environments with long equipment lifecycles.
Most critically, these systems weren’t designed for unmanned, distributed operations requiring sophisticated remote monitoring and control capabilities. Their monolithic architecture makes them difficult to scale, update, or integrate with modern business systems and cloud services.
The Renewable Energy Reality Gap
The operational context for renewable energy creates fundamental challenges that expose every limitation of traditional SCADA systems:
Distributed, Unmanned Sites: Renewable portfolios often include hundreds of remote locations without permanent on-site technical staff. These sites must operate reliably with minimal human intervention while providing comprehensive remote monitoring and control capabilities.
Cybersecurity Imperatives: NERC CIP requirements, NIS2 directives, and an evolving cyber threat landscape demand sophisticated security measures that go far beyond the physical access controls that traditional SCADA systems rely on.
Internet Traffic: Without permanent on-site technical staff, maintenance and control functions—along with all OT data destined for central repositories—now traverse Internet connections.
Critical Infrastructure Responsibilities: Renewable energy assets increasingly serve as critical infrastructure whose operational resilience can have broad impacts on grid stability beyond the immediate plant owner-operator. Essential functions such as software back-ups, asynchronous communications, remote patching must be managed and executed either—whether locally or centrally—with absolute assurance that any issues or failures will not compromise system stability or plant operations.
Rapid Technology Evolution: The renewable energy sector experiences constant equipment evolution, new integration requirements, and changing operational practices. Traditional SCADA systems, with their complex programming requirements and proprietary interfaces, cannot adapt quickly enough.
Cost Sensitivity: Thin margins in renewable energy operations require efficient, scalable solutions that minimise both capital and operational expenses. The high programming, configuration, and maintenance costs associated with traditional SCADA systems often exceed what renewable operators can economically justify.
Portfolio Diversity: Renewable portfolios typically include multiple technologies, equipment vintages, and site configurations across diverse geographic locations. Traditional SCADA’s requirement for custom programming at each site makes portfolio-wide standardisation prohibitively expensive.
Sub-systems operate largely independently: Renewable SCADA systems serve primarily as data aggregation and visualisation tools, leaving complex control logic to dedicated sub-systems such as inverters, trackers, substations, and power plant controllers.
PART 2
Digital Control Platform Evolution: A New Paradigm
Digital Control Platforms emerged from the Industrial Internet of Things movement and cloud-native architectural thinking, specifically designed to address the operational challenges that renewable energy presents.
Hardware Agnostic Architecture: DCPs can run on any Linux-capable system, from low-power industrial PCs to rackmount enterprise servers, VMs, containers, and commodity edge devices. This flexibility allows operators to choose hardware based on site requirements and cost considerations rather than vendor-specific controller limitations.
Cloud-Native Architecture: Built using microservices, RESTful APIs, and message brokers, DCPs leverage cloud-native architectural principles that enable horizontal scalability, resilient operation, and seamless integration with modern business systems.
Open Standards Foundation: Unlike proprietary SCADA controllers, DCPs utilise standards-based soft PLCs and open-source technologies like Linux. This approach eliminates vendor lock-in while providing access to a vast ecosystem of compatible tools and expertise.
Secure-by-Design Philosophy: Rather than retrofitting security onto legacy architectures, DCPs integrate cybersecurity throughout the entire data lifecycle—from source collection through central storage to sharing secured by multi-factor authentication and tailored access controls.
Elastic Cloud-Native Architecture: DCPs are typically delivered as cloud-based managed services that leverage the inherent elasticity of cloud-native systems. This elasticity enables seamless horizontal and vertical scaling to meet changing demands. In the renewable energy world, this means an Independent Power Producer can leverage a single platform as they grow from megawatts to gigawatts to someday terawatt-sized portfolios.
Multi-Function Capability: A single hardware platform can simultaneously support multiple operational functions including data collection, normalisation, local historian capabilities, and power plant controller functions.
Secure-by-Design Elements: Beyond Traditional SCADA Security
The security advantages of DCPs extend far beyond what traditional SCADA systems can achieve:
Outbound-Only Communications: DCPs eliminate inbound attack vectors by using only outbound connections from plant sites to central systems, fundamentally reducing the attack surface.
Automated Network Discovery: Continuous scanning and asset inventory capabilities provide real-time visibility into plant networks, automatically detecting new equipment connections and potential security threats.
Integrated Access Controls: Granular permission systems are built into the platform architecture rather than requiring separate security systems, reducing complexity while providing more sophisticated access control.
Encrypted Data Transit: Built-in encryption protects data transmission without performance penalties, ensuring that sensitive operational data remains secure throughout the collection, transmission, and storage process.
Simplified Remote Access: Secure remote operations capabilities eliminate the need for complex managed service provider dependencies or elaborate VPN configurations.
PART 3
Operational and Economic Advantages: The Business Case for DCPs
Faster Deployment: DCPs utilise a standardised machine plugin model where the DCP vendor builds each equipment plugin just once, which can then be reused plug-and-play anywhere that same equipment is deployed. Unlike SCADA systems that require custom programming for each installation, DCP plugins built once work everywhere, dramatically accelerating the onboarding of new plants, equipment additions like repowering or BESS installations, and even whole portfolios acquired through M&A activity.
Lower Integration Costs: Leading APM and Battery Analytics vendors already integrate with DCP APIs like Ardexa’s, eliminating custom connector development costs. This existing ecosystem integration dramatically reduces both initial integration expenses and ongoing maintenance costs.
Enhanced Security Posture: Modern cybersecurity built into the platform foundation provides superior protection compared to security measures retrofitted onto legacy SCADA systems.
Operational Flexibility: The standardised plugin architecture enables customer-configurable data collection, allowing operators to add additional data tags, modify collection frequencies, or adjust normalisation schemes without vendor involvement.
Portfolio Scalability: The standardised plugin model enables consistent approaches across diverse assets—the same inverter plugin works whether deployed at a 5MW site or a 500MW facility. This plugin standardisation enables portfolio-wide optimisation and equipment consistency that traditional SCADA systems cannot achieve without prohibitive site-by-site customisation costs.
Vendor Independence: Complete control of data from source to consumer eliminates vendor dependencies that plague traditional implementations. This data sovereignty preserves operational flexibility and negotiating leverage.
Reduced Operational Overhead: Onsite requirements are limited to physically deploying host hardware, connecting it to the network, and powering it up. Everything else is handled remotely through centralised management of all remote nodes. DCPs like Ardexa provide integrated software distribution built into the platform, streamlining updates and patching of both the nodes themselves and their plugins across entire portfolios.
The Path Forward: Strategic Considerations for Renewable Operators
The adoption of Digital Control Platforms doesn’t require replacement of existing SCADA infrastructure. DCPs complement existing plant control systems, with SCADA continuing to perform its essential role in local plant operations, particularly for larger plants.
Complementary Integration: DCPs work alongside existing SCADA systems rather than replacing them. In some cases, the DCP may replace the data acquisition service component of a SCADA solution, but there’s no need for wholesale SCADA replacement. The DCP vendor takes on the burden of integrating remote plant equipment into the overall DCP architecture remotely.
Phased Implementation: Operators can phase DCP rollouts over time while maintaining existing operations. Due to the standardised plugin approach, DCP vendors typically offer fixed implementation fees rather than the variable scoped services project approach required by SCADA implementations.
Independence Strategy: Continuing to use existing APM solutions while deploying DCPs as the primary OT data warehouse creates operational independence and strategic flexibility. DCPs’ open architecture and standards-based approach provide the foundation for maintaining vendor independence while accessing best-of-breed solutions across different operational functions.
Future-Proofing Investment: DCPs’ software-defined, cloud-native architecture provides adaptability that traditional SCADA systems cannot match for evolving regulatory requirements and operational demands.
Conclusion: The Imperative for Change
The renewable energy industry stands at a crossroads. Operators can continue to force traditional SCADA systems to fulfill a broad set of functions for which they were not designed, or they can integrate Digital Control Platforms alongside their traditional SCADA systems, for a best-in-class approach to their OT data architecture.
This isn’t just about choosing different technology—it’s about choosing an operational philosophy that prioritises flexibility over vendor dependence, security over legacy compatibility, and strategic positioning over short-term convenience.
The operators who make this transition strategically will gain sustainable competitive advantages in operational efficiency, security posture, and business agility. Those who delay will find themselves increasingly constrained by legacy architectural decisions that become more expensive to maintain and more difficult to escape over time.
The future of renewable energy operations belongs to platforms designed for renewable energy’s reality, not manufacturing’s legacy. The adoption of modern cloud-native technology in local plant SCADA systems serves as the clearest indicator of an operation’s progress toward this new paradigm.